Proper Bolt Torque
What is the Proper Torque to Use on a Given Bolt
by Joe Greenslade
"What torque should I use to tighten my bolts?" is a question suppliers of bolts are frequently asked by end user customers. Many times I have been asked if a chart is published on the recommended tightening torque for various bolt grades and sizes. I do not know of any. This article provides such a chart for "Initial Target Tightening Torque. It See Figure 1. The formula for generating these values is explained below.
The widely recognized engineering formula, T= K x D x P (to be explained later in this article), was used to provide the chart's values, but it must be understood that every bolted joint is unique and the optimum tightening torque should be determined for each application by careful experimentation. A properly tightened bolt is one that is stretched such that it acts like a very ridged spring pulling mating surfaces together. The rotation of a bolt (torque) at some point causes it to stretch (tension). Several factors affect how much tension occurs when a given amount of tightening torque is applied. The first factor is the bolt's diameter. It takes more force to tighten a 3/4-10 bolt than to tighten a 318-16 bolt because it is larger in diameter. The second factor is the bolt's grade. It takes more force to stretch an SAE Grade 8 bolt than it does to stretch an SAE Grade 5 bolt because of the greater material strength. The third factor is the coefficient of friction, frequently referred to as the "nut factor." The value of this factor indicates that harder, smoother, and/or slicker bolting surfaces, such as threads and bearing surfaces, require less rotational force (torque) to stretch (tension) a bolt than do softer, rougher, and stickier surfaces. The basic formula T = K x D x P stated earlier takes these factors into account and provides users with a starting point for establishing an initial target tightening torque.
• T
|
Target tighten torque (the result of this formula is in inch pounds, dividing by 12 yields foot pounds |
• K
|
Coefficient of friction (nut factor), always an estimation in this formula |
• D
|
Bolts nominal diameter in inches |
• P
|
Bolt's desired tensile load in pounds (generally 75% of yield strength) |
The reason all applications should be evaluated to determine the optimum tightening torque is that the K factor in this formula is always an estimate. The most commonly used bolting K factors arc 0.20 for plain finished bolts, 0.22 for zinc plated bolts, and 0.10 for waxed or highly lubricated bolts.
The only way to properly determine the optimum tightening torque for a given application is to simulate the exact application. This should be done with a tension indicating device of some type on the bolt in the application. The bolt is tightened until the desired P (load) is indicated by the tension indicating device. The tightening torque required to achieve the desired tension is the actual tightening torque that should be used for that given application. It is extremely important to realize that this tightening value is valid only so long as all of the aspects of the application remain constant Bolt suppliers sometimes have customers say that their bolts are no good because they have started breaking while being installed. Thorough investigation commonly reveals that the customer has started lubricating the bolts to make assembly easier, but maintained to same torque as was used when the were plain finished
The table in this article shows that by using this formula a 1/2-13 Grade 5 plain bolt should be tightened to 82 foot pounds, but the same bolt that is waxed only requires 41 foot pounds to tighten the same tension. A perfect 1/2-13 Grade 5 waxed bolt will break if it is tightened to 81 foot pounds because the K factor is drastically lower. The bolts are fine, but the application changed. Suppliers need to understand this and be able to educate their customers to resolve this common customer complaint about breaking bolts. The chart is provided for quick reference by fastener suppliers and users for selecting an initial target tightening torque. This chart was derived by using the formula shown earlier. An example of the calculation is as follows: |
||||||||||||||
|
||||||||||||||
Hopefully the chart will help suppliers with an initial answer to the customer's question, "What torque should I use to tighten my bolts?" Keep in mind this is only an estimated value. It may provide satisfactory performance, but it also may not. Every application should be evaluated on its own to determine the optimum torque value for each application. Major bolt suppliers should have tension indicating equipment necessary to help their customers determine the appropriate tightening values for their specific applications. Keep in mind that if the lubricant on a bolt and nut combination is changed, the tightening torque value must be altered to achieve the desired amount of bolt tension. | ||||||||||||||
Joe Greenslade is President of Greenslade and Company, Inc. located in Rockford, Illinois. His firm specializes in providing manufacturing tooling and inspection equipment to suppliers of screws, bolts, rivets, and nuts throughout the world. Joe is an inventor, author, and lecturer. He holds eleven US Patents. Has written over 80 technical articles for industrial trade journals, and has spoken frequently at trade association meetings and technical conferences on issues related to industrial quality for the past ten years. He is an Associate Member of the Industrial Fastener Institute and a member of the American Society of Mechanical Engineers B1 Thread Specification Committee. In 1992, Joe was recognized for his technical and innovative contributions to the fastener industry when, at age 44, he became the youngest person to be inducted into the National Industrial Fastener Show "Hall of Fame. " |
If you do not see what you are looking for or need more information, please contact us we will be happy to help you!
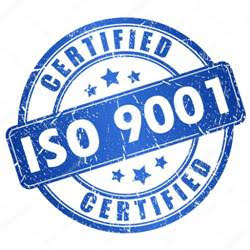
219 Baywood
Houston TX 77011
Toll Free: 800-991-1280
Fax: 713-675-6066
Local: 713-675-0123